How Alcon implemented the Pozyx RTLS solution with eye for detail
Alcon assembles thousands of unique surgical packs and was looking for an efficiency tracking system to monitor operator efficiency and to build in flexibility with changing team sizes and varying production flows for their dynamic product portfolio. The final solution, based on the Pozyx RTLS (real-time location system), resulted in the creation of an efficiency dashboard to optimize operator work output and is used as input to the finance department to evaluate labor cost and improve cost calculations.
Alcon is the largest eye care device company in the world and has a 70-year history in helping people see better. Founded in the U.S. and headquartered in Geneva, Alcon’s reach is truly global with facilities in over 70 countries. The company focuses on two clear fields: surgical equipment and contact lenses. At the forefront of Alcon’s success is a commitment to “cutting-edge innovation and breakthrough technology”. Its operation in Puurs, Belgium, takes this forward-looking mentality to heart by implementing the Pozyx RTLS based track & trace solution to help their operators excel in their day-to-day tasks and to provide real-time efficiency data to optimize cost calculations.
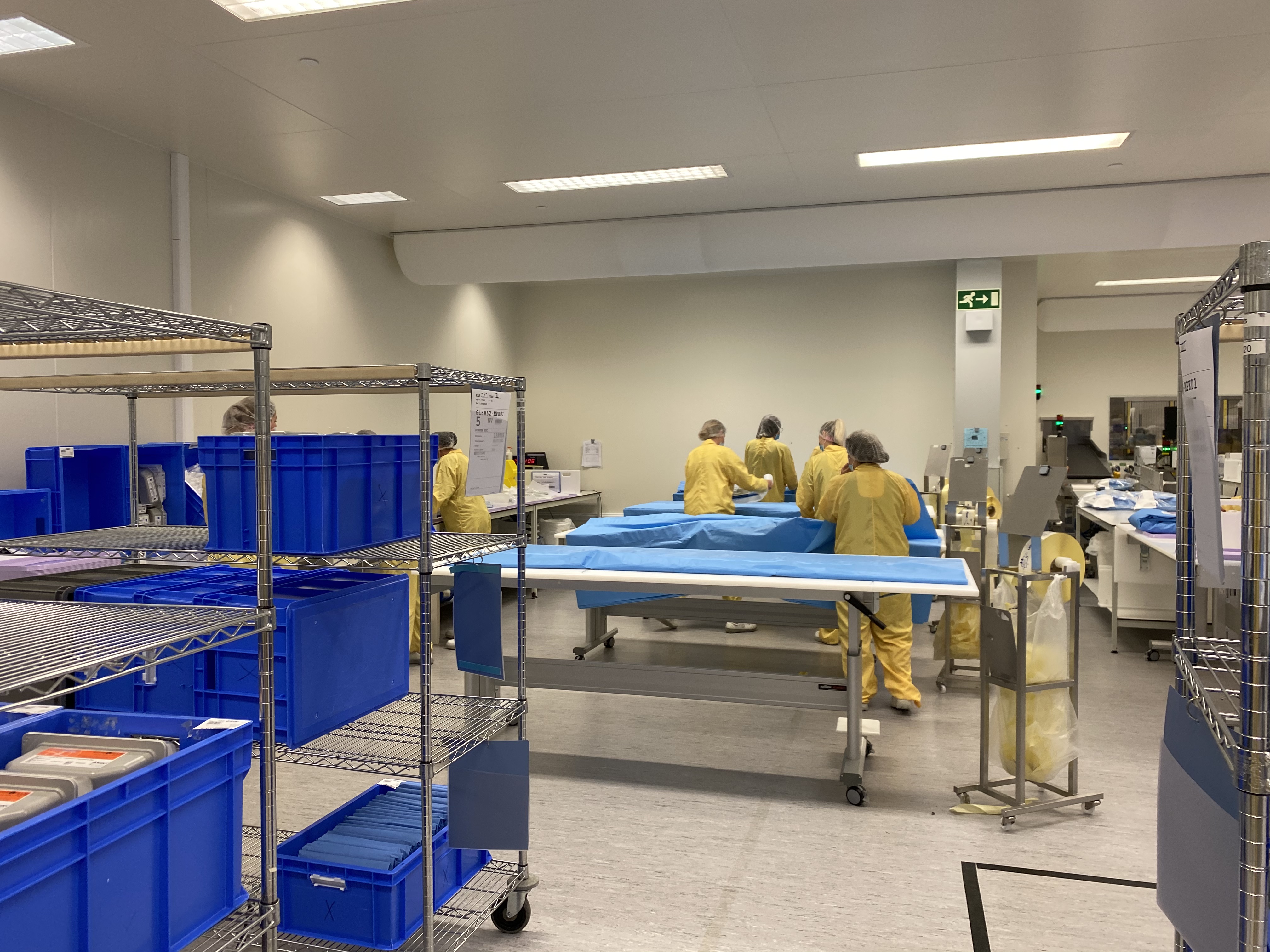
A blurry vision on efficiency and cost
At the Alcon facility in Puurs, surgical packs with ophthalmic instruments and products for various eye-related conditions are bundled and shipped to hospitals. These packages are known as Custom Paks and are highly tailored to the customer’s needs and the surgeon’s individual preferences. This results in thousands of product variations, which are assembled semi-automatically.
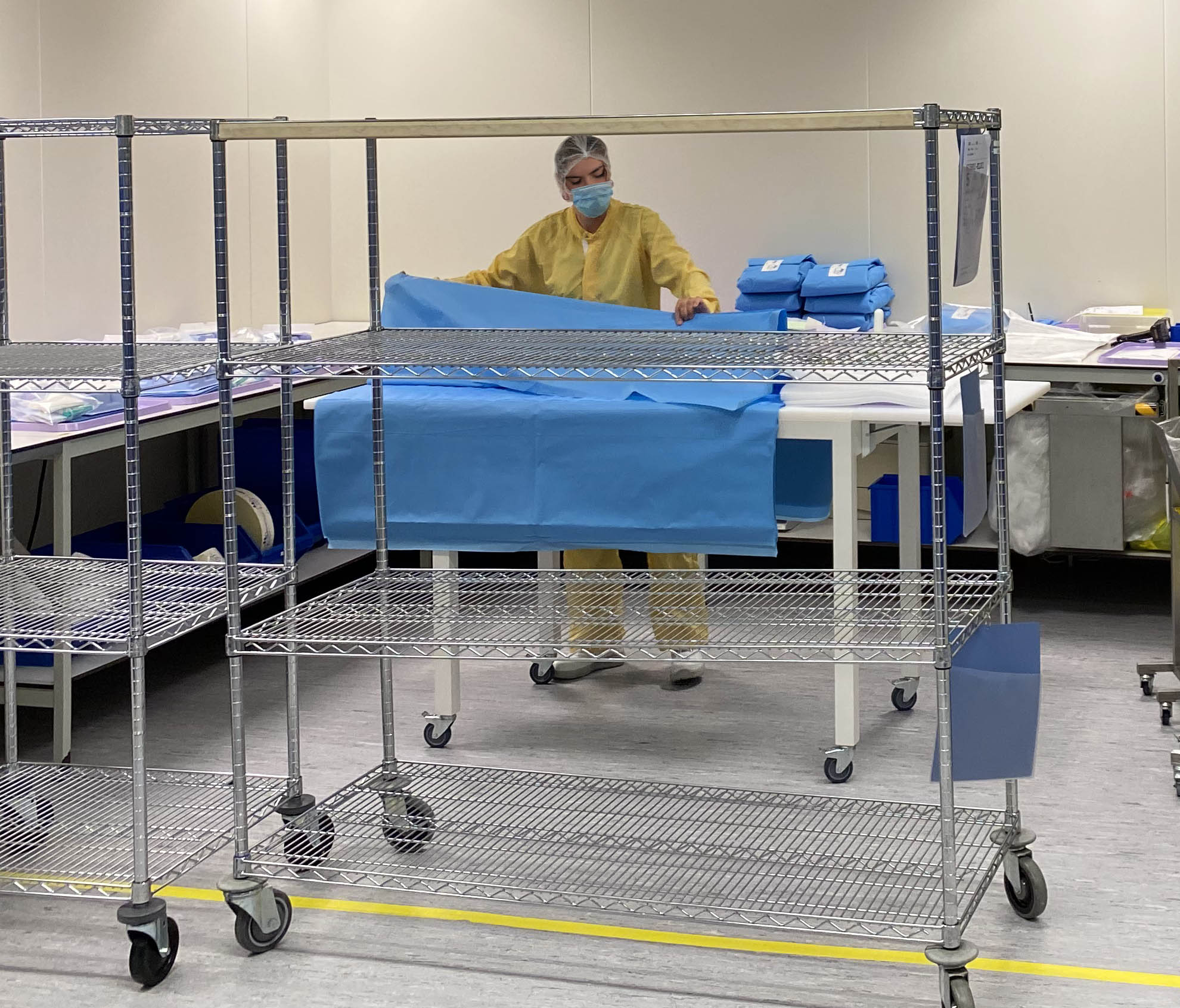
The result is a complex order and BOM list linked to a complicated assembly process, with over 40.000 unique combinations of components per order. This makes it difficult to quantify output in terms of cycle times, cost, and efficiency. One of the key challenges is to provide the finance department with accurate data on labor cost to be able to make better decisions on price setting and product profitability. A detailed understanding of labor cost per specific order is lacking.
The production is executed by about 300 operators, working in three shifts (limited night shift). Line managers take charge of order prioritization and instruct the operators on the shop floor. But because the production process is complex and dispersed, it is difficult to monitor the status of partial orders. It can happen that partial orders which are stuck down the line, keep shipments from going out. This leads to expediting orders and pulling operators away from their original planning to work on these priority orders.
This efficiency challenge adds to the complexity of monitoring labor time, and in turn impacts the cost per order calculation. That is why Alcon decided to look for future-proof efficiency tracking, dashboard and reporting solutions. The reporting tool was required to have real-time capabilities and a focus on Operator Efficiency and production line output. Their search led them to Enginity and Pozyx, but some challenges had to be overcome to turn the project into a success.
Why Ultra-Wide Band?
As is the case with many IoT or Industry 4.0 projects, Alcon researched different technologies to match their needs. Barcode and RFID badge stations were considered not flexible enough for installation. And people forgetting to badge in or out would still generate unreliable data. UWB (ultra-wideband) provided the answer to these concerns, but there were still additional considerations that made the Alcon project extra challenging.
For starters, the controlled environment. The facilities operate mostly within clean rooms where stringent cleaning and disinfection regulations are observed. Testing revealed that the standard Pozyx IP 66/67 Anchor casings - that normally protect against powerful water jets and immersion - were not able to withstand the specific and aggressive cleaning agents that Alcon uses. Custom casings, using an even more robust plastic, were developed and produced to shield the Anchors from these chemicals.
And of course, there was the constraint of not impeding production during installation. Since Alcon runs in shifts, this meant the installation had to happen after production hours. With cabling and anchors being installed in less than four days, there was virtually no impact on the production schedules.
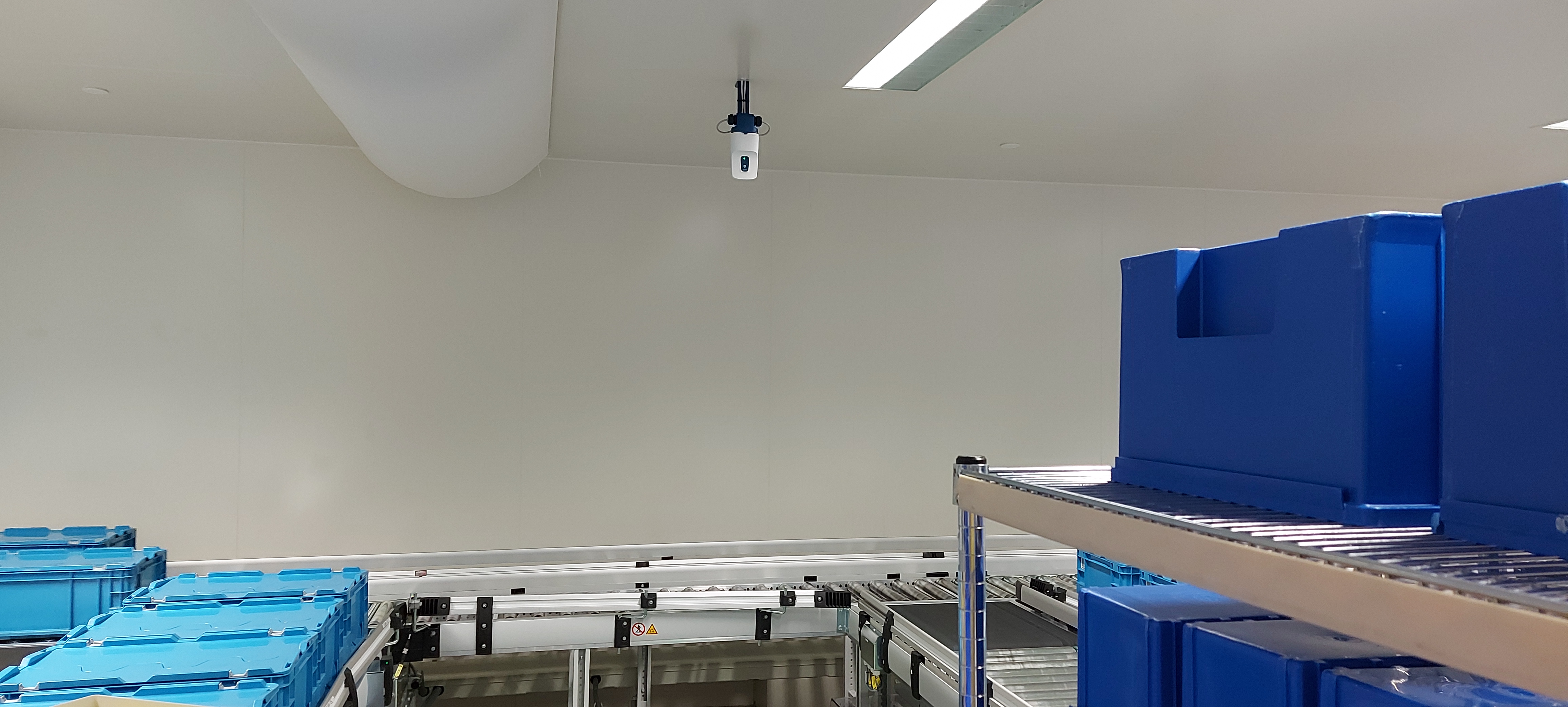
Human challenges and embraced solutions
The final and most important hurdle was without doubt the sensitive issue of tracking people on the job. Alcon decided wisely to involve all stakeholders from the get-go and clearly communicate about why and how of the efficiency tracking system. Both the management teams and the unions were involved from the start. Key to addressing the sensitivities and privacy concerns was to highlight that tags work anonymously. Alcon wanted to focus on the efficiency per production station and the number of employees per station and did not want to relate to the efficiency of individual operators. All tags are randomly assigned and work on an ID basis, which is not linked to individuals.
The project team even took to the shop floor to meet with every single operator in small groups to meticulously explain the reasons and goals of the project. They involved operators for trials and invited them to validate the product choices.
“Operators were really concerned at first. But after explaining the technology and the goals of the project, support followed quickly. A number of operators spontaneously volunteered for the first trials,”
said Kevin Braeckmans – Process Efficiency Engineer
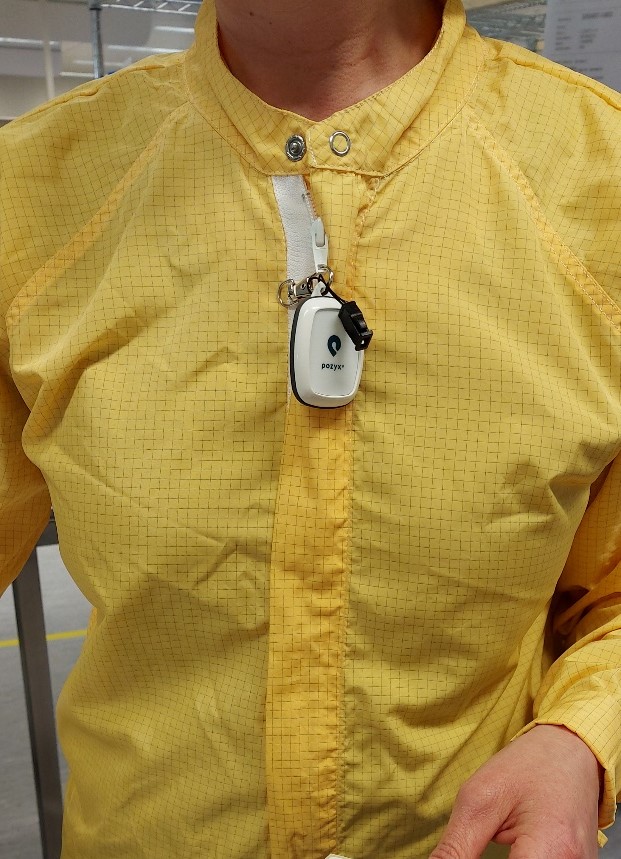
Following the trials, the response from employees was collectively positive. They initiated a brainstorming session and came up with creative new features for the Pozyx system. The successful implementation would not have been possible without the valuable support and insights of all stakeholders involved.
Real-time productivity visualized
The Pozyx RTLS was implemented to cover the shop floor of with a total of 31 anchors. At the start of their shift, the 300 operators receive a random Pozyx tag that they will wear during that day. Virtual zones in the Pozyx web app match the physical location of workstations. This allows Pozyx to collect, track, and report how much time employees spend in each workstation to a software platform developed by Enginity.
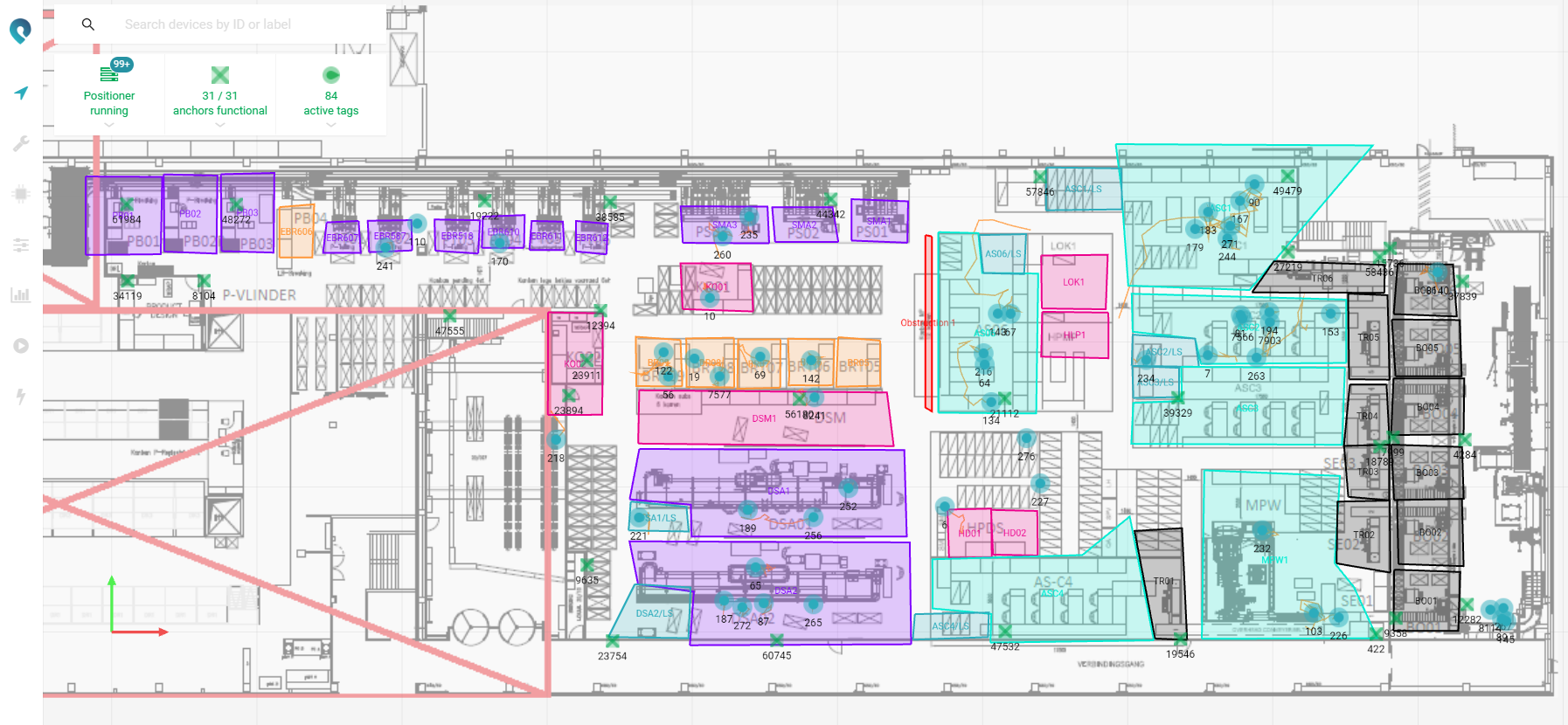
The platform monitors and reports in real-time how many operators are currently working at a workstation. The ERP system adds information on which order is being processed. By combining these two data streams, Enginity developed a dashboard that indicates the efficiency of workstations in real-time.
“In the past, we were not able to detect efficiency issues in real-time. This only became visible on the line itself or the next day, when reports about the previous day’s production were sent out manually. With the solution from Pozyx and Enginity we no longer have to wait for the facts, but we can detect issues in real-time and, take immediate action to solve them!”
stated Kevin Braeckmans – Process Efficiency Engineer
With the Pozyx real-time monitoring capabilities Alcon expects an ROI between 24 and 36 months. Although this may seem like a very long time for an IIoT implementation, the biggest chunk of the investment is reserved for the development of the software platform. Considering that this platform will also enable other capabilities such as more accurate reporting of production cost, the investment is expected to level much faster.
All eyes on the price
In fact, the real-time capabilities of the efficiency tracking system are just the starting point for Alcon. The bigger benefit is in achieving more accurate cost calculation for their finance department. A plan has been developed to reach that ultimate goal, and Pozyx provides only the first step in implementing a more data-driven reporting standard.
Testimony to the value of the Pozyx solution is the nomination for a program at Alcon that finds and rewards internal innovation projects. It is not just a validation of the technological innovation, but also an award of the vision that the team has developed to keep up with the ever-evolving landscape of manufacturing and assembly. With Enginity and Pozyx at their sides, the team at Alcon is convinced that they have found the cure for their blurred vision.
Conclusion
The Pozyx RTLS system based on UWB is the cornerstone of a full-fledged Efficiency Tracking System that allows Alcon to monitor and optimize complex assembly lines for diverse product portfolios in combination with the challenges of unpredictable operator team sizes. The real-time reporting and the efficiency dashboard allow instant interventions and avoid problems down the line which can result in having to launch expensive expedite orders. The finance department will finally be able to assess labor cost per order and optimize prize calculations. In short, Alcon now has a clear view of one of its most complex assembly lines.
Please schedule a demo to find out how the innovative Pozyx location solutions can boost your business with real-time and dynamic positioning analytics.