Work in Progress (WIP) Tracking
Efficiently managing and reducing Work in Progress (WIP) levels is essential for optimizing manufacturing workflow efficiency and maintaining lean manufacturing techniques. The Pozyx RTLS system offers comprehensive WIP tracking by monitoring assets throughout the entire production process—from raw materials to finished products. This real-time visibility enhances material flow management, providing detailed insights into job orders and production cycle times. With accurate data on work in progress inventory, manufacturers can identify bottlenecks, improve production process optimization, and ensure supply chain visibility for better operational efficiency.
Book a demoEnhancing shop floor visibility is crucial for optimizing production workflows and reducing unnecessary delays. Pozyx’s real-time tracking solutions provide complete transparency into orders, operators, and equipment.
Pozyx’s real-time tracking system monitors orders, operators, and equipment throughout the entire production process, reducing labor costs and eliminating time wasted on manual scanning. This enhanced visibility allows teams to:
- Effortlessly track order status and workflow progess
- Quickly locate priority orders and necessary equipment
- Streamline production workflows and reduce bottlenecks
With accurate, real-time insights into work in progress (WIP), companies can minimize delays, improve material flow efficiency, and boost overall productivity. Pozyx also enables customized dashboards to enhance production oversight, provide accurate lead times, and deliver transparent updates to customers, supporting better decision-making and workflow management.
In dynamic production environments, early detection of issues is critical to maintaining efficiency and quality. Pozyx’s real-time tracking system helps identify problems before they impact workflows.
Pozyx’s tracking technology allows manufacturers to define custom rules for issue detection, ensuring immediate identification of potential problems. The system can trigger real-time warnings for scenarios such as:
- Buffers overflowing or running empty
- Orders deviating from predefined workflows
- Materials or equipment remaining idle for too long
These proactive alerts help minimize production delays and improve workflow efficiency. Organized dashboards deliver instant insights, enabling teams to quickly resolve issues and make data-driven decisions. By addressing problems as they arise, companies maintain productivity, ensure quality standards, and keep material flow smooth and uninterrupted.
Precise labor tracking is essential for understanding production costs and identifying inefficiencies. Pozyx’s real-time tracking system provides accurate insights into labor allocation across the shop floor.
In production environments with high variability and manual labor, tracking labor time for each step can be challenging. Pozyx’s system measures the actual bill of labor by tracking operators and orders in real time. This granular visibility helps manufacturers:
- Accurately calculate labor costs for each production step
- Identify inefficiencies and bottlenecks in workflows
- Optimize labor allocation to reduce waste
With detailed labor data, companies can assess profitability at the product or order level, improve cost management, and enhance resource allocation. These insights support informed decision-making, ensuring more efficient operations and improved overall production profitability.
Maximizing efficiency in make-to-order (MTO) and quick response manufacturing (QRM) environments requires managing variability and optimizing resources. Pozyx’s RTLS delivers the insights needed to streamline every aspect of production.
Pozyx’s real-time location system (RTLS) captures efficiency data to support lean transformation and continuous improvement, even in advanced QRM setups. By enhancing key metrics such as takt time, operator efficiency (OOE), and overall equipment effectiveness (OEE), Pozyx helps companies:
- Minimize operational variability
- Streamline workflows and eliminate bottlenecks
- Optimize resource allocation and reduce waste
By addressing the eight wastes in lean manufacturing, Pozyx drives faster response times, lowers production costs, and improves adaptability to customer demands. This results in a more efficient, flexible, and cost-effective production process.
Maintaining a safe and compliant work environment is critical in manufacturing. Pozyx’s real-time tracking system ensures operators follow safety protocols and regulatory standards.
Pozyx’s tracking system monitors operator movements and ensures adherence to safety guidelines and regulatory standards. Supervisors can track proper equipment use, maintain safe distances, and receive real-time alerts if an operator:
- Enters a hazardous area without authorization
- Uses equipment without the required training
- Violates predefined safety protocols
By proactively identifying and addressing safety concerns, Pozyx helps reduce the risk of workplace incidents and fosters a culture of safety. This enhanced safety monitoring supports regulatory compliance, minimizes potential hazards, and reduces liabilities, ensuring a safer and more secure work environment.
Staying ahead of potential issues is key to maintaining seamless production. Pozyx’s automated alerts and notifications keep your workflows on track with real-time updates.
Pozyx’s system allows manufacturers to set up automated alerts and notifications for critical conditions, such as low inventory levels, idle equipment, or workflow deviations. These real-time alerts help teams:
- Quickly respond to production issues
- Prevent bottlenecks and delays
- Ensure smoother workflow continuity
By minimizing the need for manual monitoring, Pozyx enables teams to focus on strategic tasks and proactive decision-making. This automated notification system improves responsiveness, reduces downtime, and supports a more efficientand resilient production process.
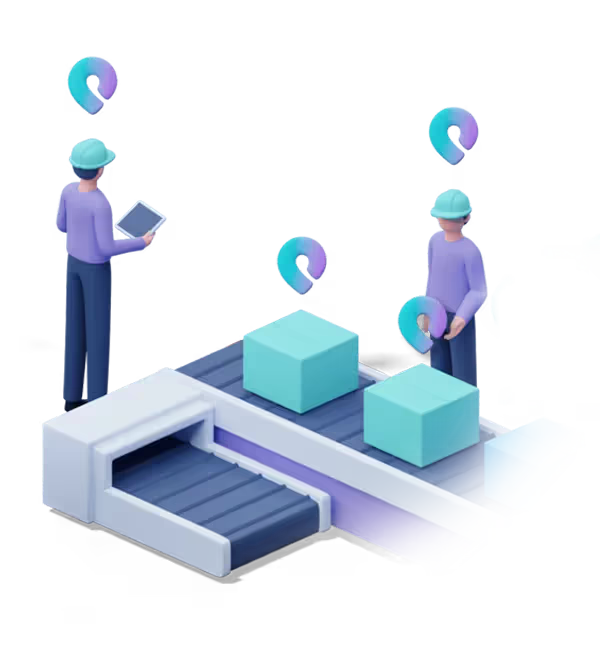
Pozyx Applications for
WIP & Material Flow Optimization
Optimizing Work in Progress (WIP) and material flow is essential for efficient manufacturing. Pozyx's real-time location tracking solutions provide complete end-to-end process visibility and actionable insights to streamline production. From monitoring inventory levels to automating workflow triggers, Pozyx helps manufacturers eliminate bottlenecks, improve quality control, and implement continuous improvement strategies. Explore how Pozyx’s RTLS technology can enhance every stage of your production process.
- End-to-End Process Visibility: Gain comprehensive, real-time insight into every stage of the production process, from raw materials to finished goods. Pozyx’s WIP tracking system ensures complete material flow visibility, allowing manufacturers to make proactive adjustments, optimize workflows, and eliminate inefficiencies. This transparency enhances production process optimization and supports lean manufacturing practices.
- Enhanced Workflow Efficiency: Streamline production sequences and reduce bottlenecks by accurately tracking material flow throughout the facility. Pozyx’s RTLS technology ensures smooth transitions between workflow stages, improving manufacturing workflow efficiency and increasing overall productivity. Optimize routes, reduce delays, and achieve seamless work in progress management.
- Accurate Inventory Tracking: Maintain precise records of inventory levels at each stage of production to avoid shortages or overstocking. Pozyx’s inventory tracking solutions provide real-time data to improve inventory management and reduce waste. This ensures that materials are always available when needed, supporting an efficient and optimized material flow.
- Real-Time Quality Control: Monitor product quality at every step with real-time data and immediate feedback. Pozyx’s RTLS system helps detect defects early in the production process, reducing waste and ensuring products meet the highest standards. Enhance your quality control processes and deliver consistent, high-quality output through proactive monitoring.
- Automated Process Triggers: Set up location-based automated triggers to streamline workflow stages. Pozyx’s RTLS technology can trigger replenishment alerts, assign tasks, or initiate specific processes with minimal manual intervention. These automations reduce human error, ensure timely task execution, and keep your production process running smoothly and efficiently.
- Historical Analysis for Continuous Improvement: Leverage historical tracking data to identify trends, measure performance, and implement continuous improvement strategies. Pozyx’s analytics provide valuable insights into WIP levels, material flow patterns, and workflow bottlenecks. Use these insights to refine processes, enhance efficiency, and drive long-term success in your manufacturing operations.
Key Performance Indicators for WIP & Material Flow
Tracking key performance indicators (KPIs) is essential for improving Work in Progress (WIP) and material flow efficiency. With Pozyx's RTLS solutions, manufacturers achieve measurable results, including reduced cycle times, lower WIP inventory levels, and faster production throughput. These insights drive continuous improvement, helping streamline workflows, enhance quality control, and minimize delays.
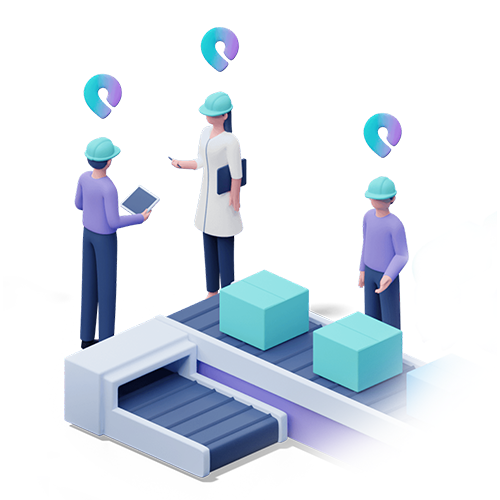
reduction in time spent monitoring the floor
better bill of labor estimation
decrease in WIP inventory levels
improved labor efficiency
faster detection of issues
decrease in workplace incidents
*Performance improvements are based on specific customer implementations and may vary by application.
Get Started now
with the Pozyx UWB Starter Kit
A Pozyx UWB Starter Kit is your gateway to advanced real-time location tracking. Equipped with high-precision ultra-wideband (UWB)technology, this kit provides everything you need to explore indoor positioning, test RTLS applications, and unlock insights for enhanced operational efficiency. Perfect for businesses seeking scalable location solutions.
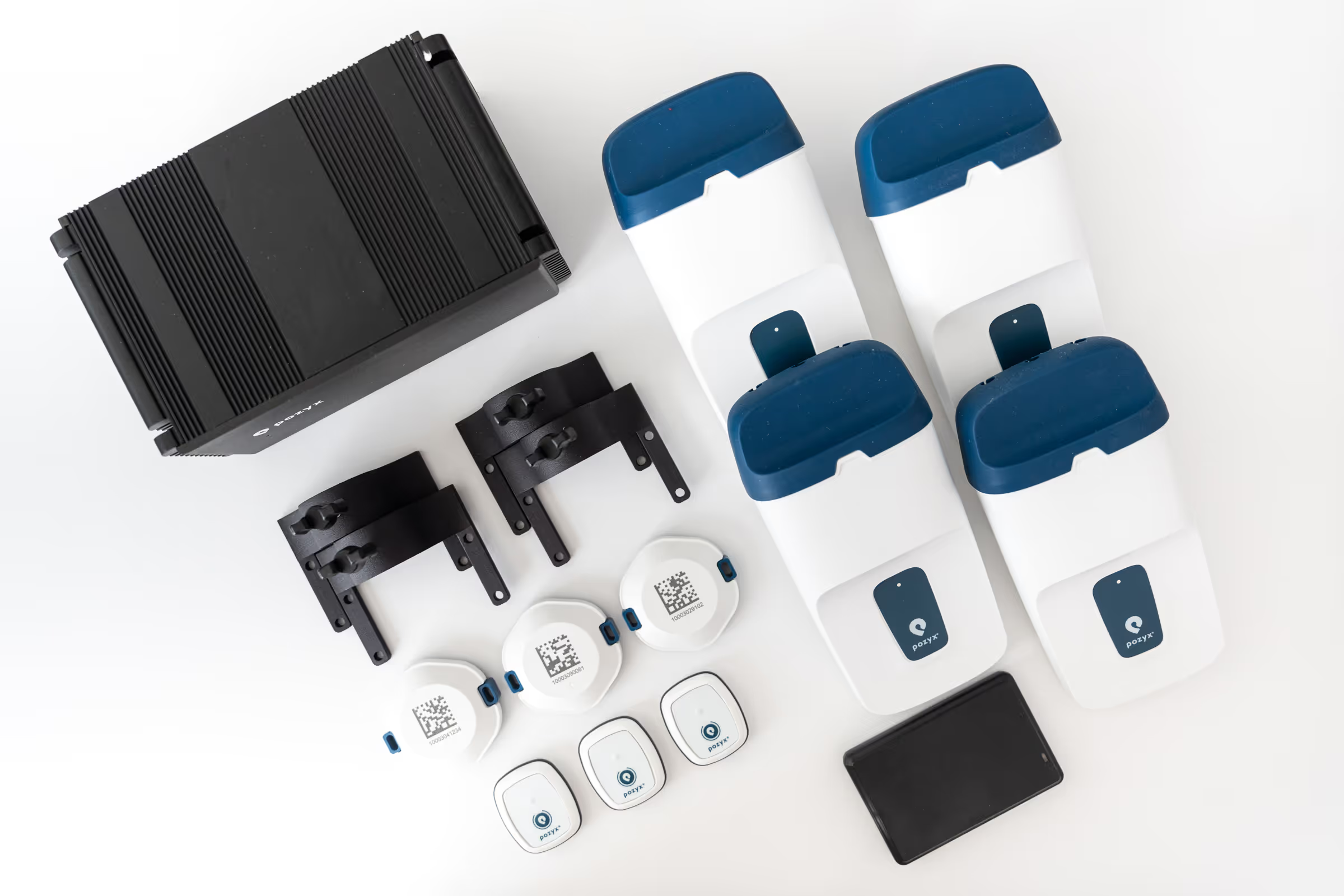