Real-time forklift tracking in an assembly plant for heavy trucks
Introduction
In an increasingly complex manufacturing environment, optimizing logistical flows is imperative for productivity and safety. Our customer, an assembly plant for heavy trucks, faced challenges with crowded factory floors and inefficient traffic management. The factory’s logistics Manager recognized the potential of Real Time Location System (RTLS) technology to alleviate these issues. Following a successful Proof of Concept in 2021, the company sought to implement a comprehensive RTLS solution to improve logistical operations.
In 2023, the rollout started in two production facilities in Europe to enable accurate tracking on both the factory floor and in the warehouse. The largest installation of the two, spanning over 35.000 sqm is covered by 250 anchors and has approximately 100 pieces of moving equipment to be tracked with the Pozyx UWB RTLS.
Quote from the Project Leader:
"Increasing traffic intensity and spatial constraints necessitated a transformative solution for our logistical challenges. RTLS offers us the tools to enhance productivity and safety within our factory."
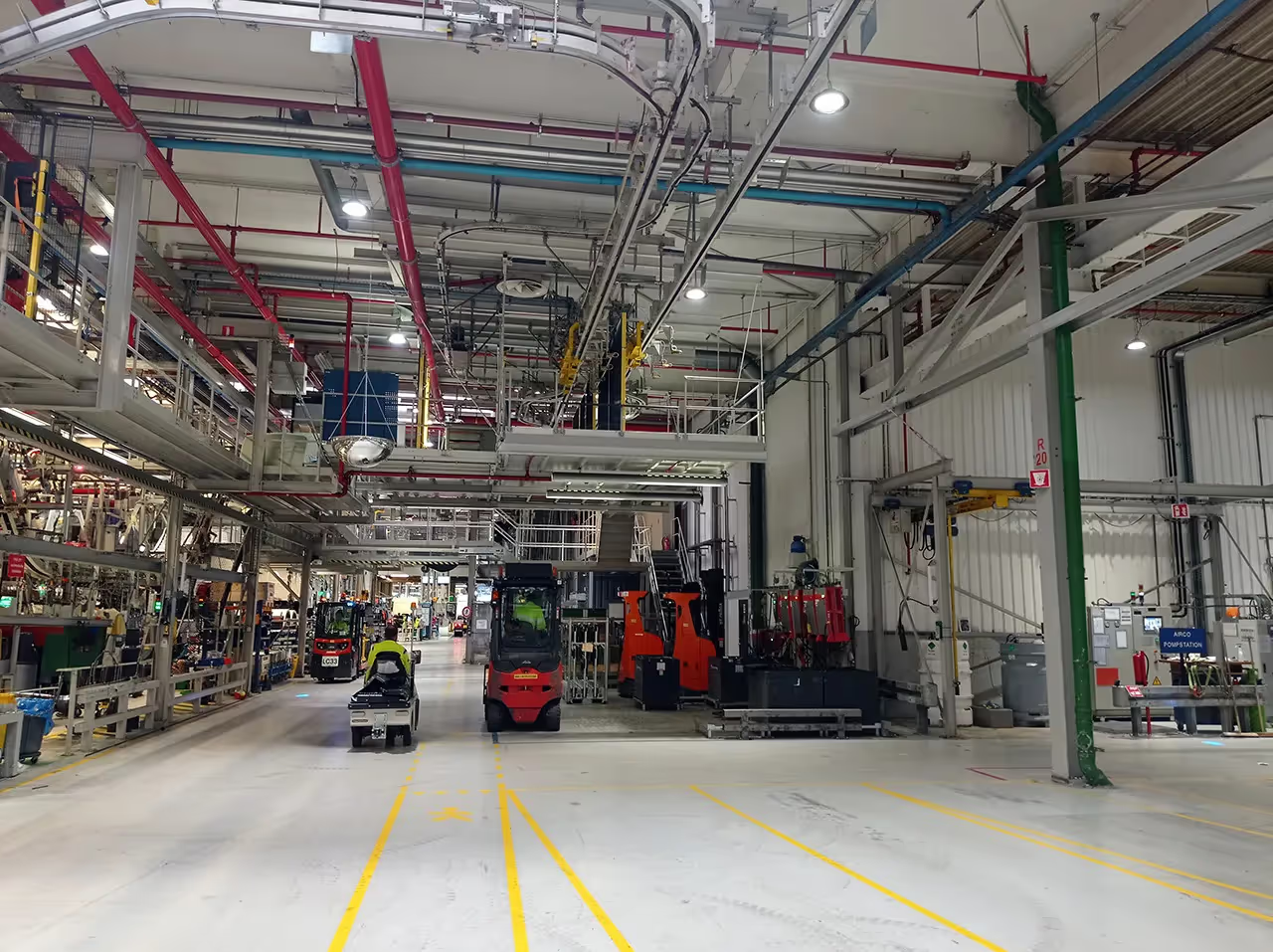
Assignment Overview
The assignment focused on implementing an RTLS infrastructure to track material handling equipment, including forklifts, order pickers, reach trucks, and tugger trains. The primary objective was to reduce traffic congestion, enhance process visibility, and improve operational efficiency.
Some of the concrete initial use-cases were:
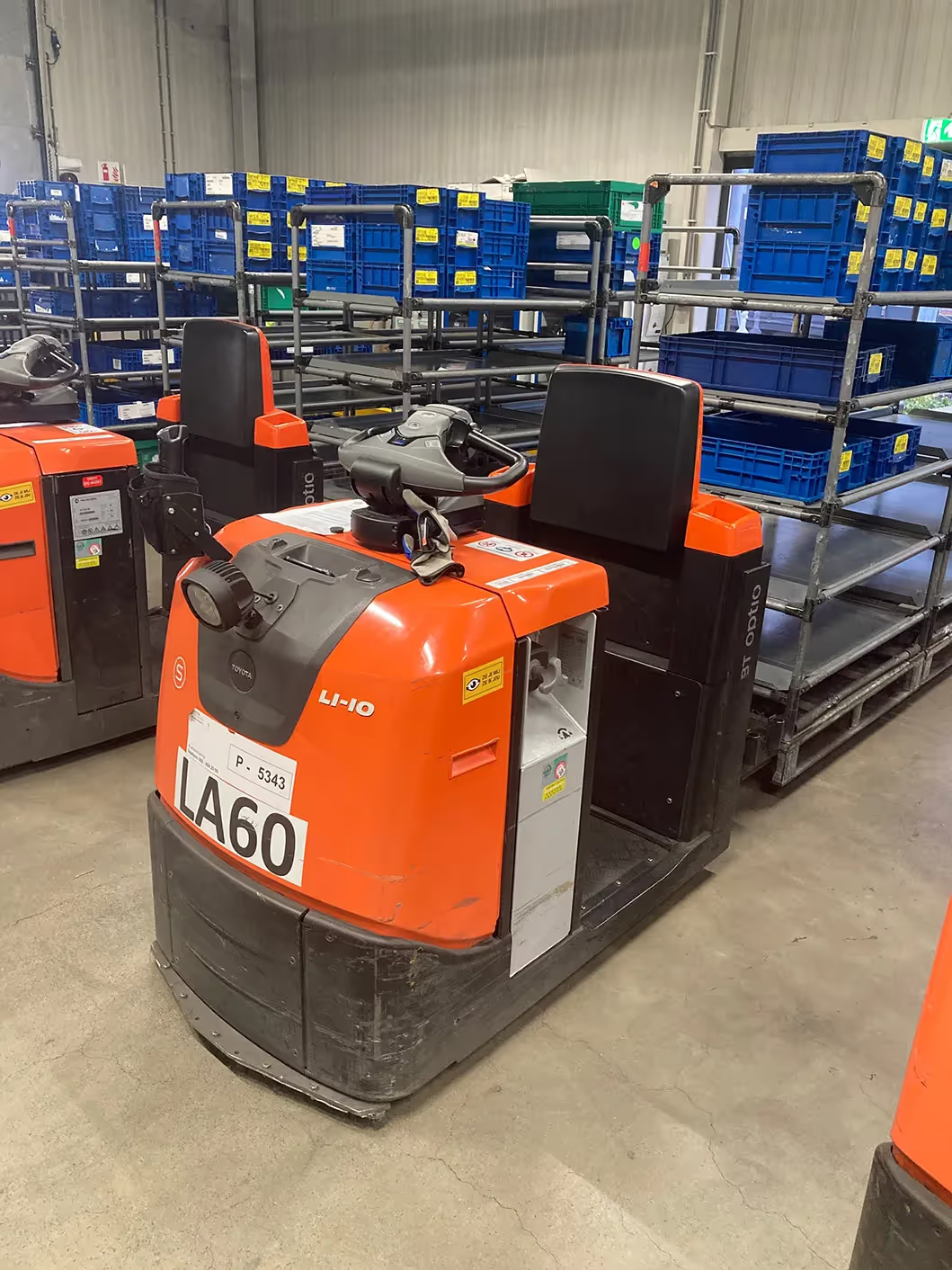
1. Forklift OEE
Due to the complex logistical flows, it becomes difficult to asses the performance of the fleet. The RTLS allows measuring the OEE (Overall Equipment Effectiveness) for all equipment to provide a comprehensive view of fleet operations. It allows users to monitor the total operation time of the fleet and its components, facilitating comparison of metrics such as run/stop time, distance traveled, and loaded/unloaded trips to optimize fleet utilization. A data dashboard aids in identifying redundant assets and offers an instant visual summary of movement over a specified time period, enabling efficient decision-making and resource allocation.
2. Data driven decision making
Due to the continuous need to improve efficiency of the factory there is a critical need for data-driven decision-making to address operational challenges effectively. Equally important as obtaining accurate data is the ability to obtain actionable insights from this data.
The RTLS replay function, spaghetti diagram, and heat map provide valuable insights for optimizing fleet movement. They reveal traffic density and bottlenecks, enabling efficient route planning. Additionally, the replay function allows users to select and review the path of any moving object at a specific time in the past, offering context to prevent incidents in the future. These tools enhance operational efficiency and support proactive decision-making in fleet management.
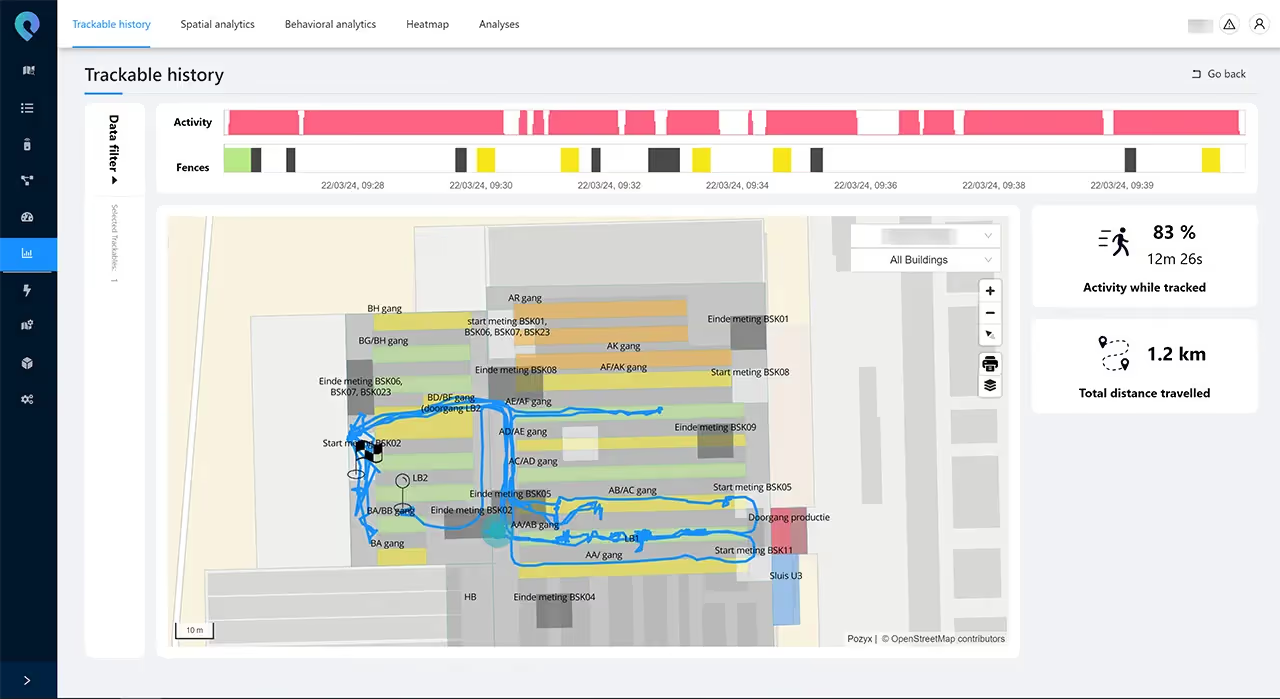
3. Elimination of concentrated traffic flows
A lot of parts are supplied just-in-time with the material handling equipment. Especially the tugger trains follow a fixed route and a takted flow. Therefore, the traffic intensity in the warehouse and factory is high. The operators start each shift from the warehouse. Also, during breaks the operators go back to the warehouse together with the material handling equipment. Therefore, at the end/start of a shift, and just before/after breaks, the flows are concentrated at one point, causing unsafe situations and traffic congestion.
It is foreseen that with RTLS, the operator is able to leave its equipment behind during breaks or at the end of the shift. With a live map, operators can find the equipment back easily. This use-case is foreseen to be implemented by adding additional screens on the factory floor to indicate equipment locations.
RTLS Requirements
Infrastructure Requirements
The RTLS infrastructure was designed to cover the extensive logistical paths within the factory and warehouses, ensuring accurate location updates with minimal interference to existing infrastructure. Specifications demanded a location accuracy of ≤ 0.5 meters and a refresh rate of ≤ 0.5 seconds.
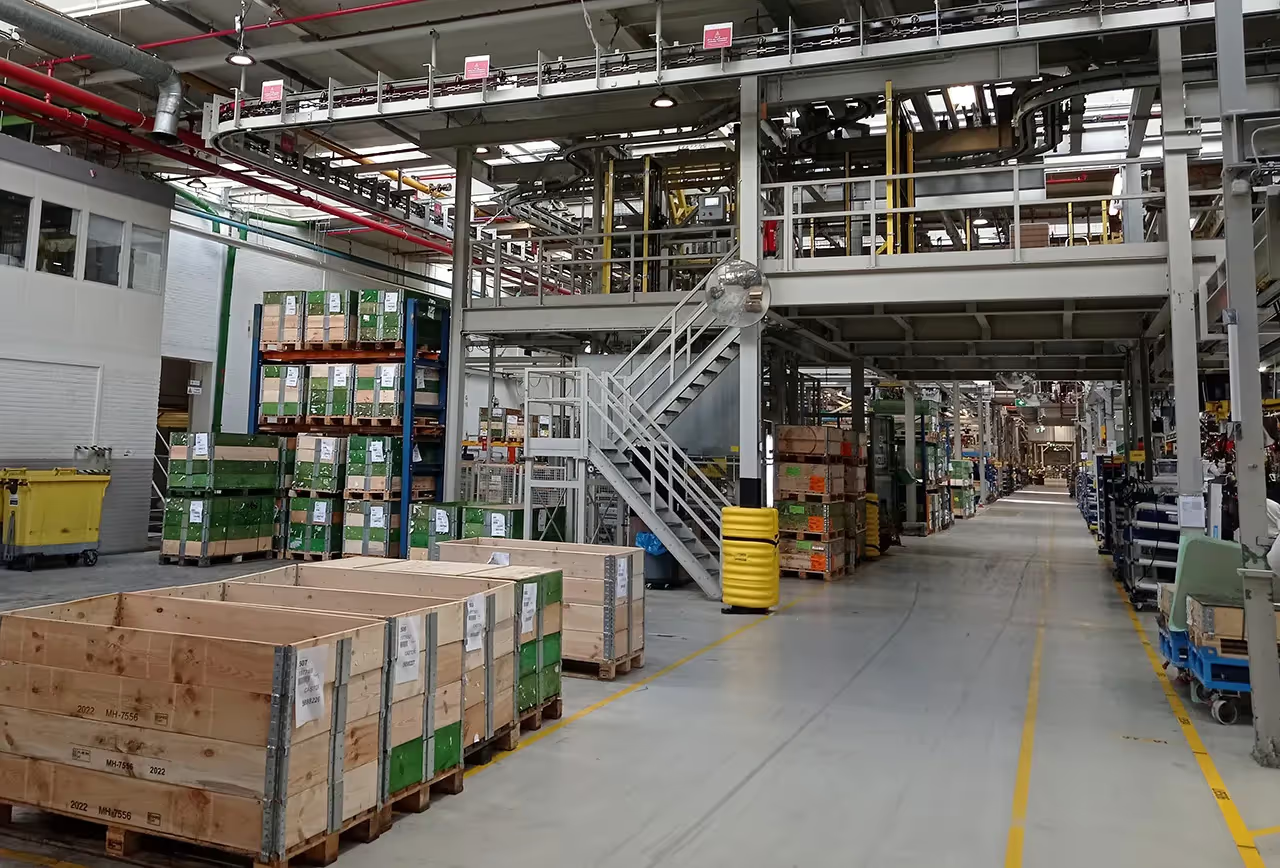
Hardware Solution
CE-marked hardware components were required, including receivers powered by Power over Ethernet (PoE) and tags resistant to outdoor conditions. Battery-powered tags needed to accommodate a minimum operational lifespan under specified conditions. The solution aimed for scalability to support at least 500 tags.
Software Solution
Functional requirements included If/then logic based on geofencing, heat maps, spaghetti diagrams, live maps, and replay functions for analyzing traffic patterns and optimizing operations. Technical specifications mandated high uptime (>99.95%) and support for low-code functionalities to facilitate internal adjustments and additions.
IT Requirements
Information security considerations mandated an on-premises software solution with stringent access controls and data ownership by the company. Communication mechanisms required RESTful API support, with additional capabilities such as MQTT and OPC-UA considered desirable.
Why Pozyx
After the proof-of-concept, an extended request for proposal (RFP) was organized for the full implementation of the system. Out of 5 providers, Pozyx was selected to provide the full RTLS solution for two of its production facilities across Europe.
Apart from meeting the requirements outlined above, the following points were considered the differentiating factors choosing for Pozyx:
- Daisy chaining of the anchors, limiting network cabling
- Open Omlox hub API support
- On-premise security
- Cost-effective solution
Conclusion and future outlook
Pozyx RTLS technology was selected to tackle a variety of challenges to streamline logistical operations, increase visibility on the intralogistics and enable data-driven decision making. The Pozyx solution addressed infrastructure, hardware, software, and IT requirements to deliver a robust and scalable system tailored to the unique needs of the manufacturing environment.
For our client, the implementation of RTLS enables a multitude of potential applications, with those outlined above serving merely as an initial glimpse. Envisioning a phased deployment strategy, the client aims to progressively leverage RTLS capabilities, commencing with non-production-critical scenarios, advancing to production-critical tasks, and ultimately integrating safety-sensitive applications. This strategic roadmap underscores the client's commitment to harnessing the full spectrum of RTLS benefits over time.
Looking to improve your intralogistics through RTLS?
Look no further! Schedule a call with our experts to discuss your use-case, we are happy to help!