Material and Information Flow analysis (MIFA) case
P3T, LLC is a US solution implementation company focused on bringing innovative ideas to reality. Their operational experience coupled with many years of Lean Manufacturing and Facility Leadership make them a great asset to any company. Industry 4.0 and the drive for reduced cost allow P3T, LLC to bring innovative technology solutions in to any Manufacturing Operation or Distribution Facility.
Contract and Scope Review
11 facilities throughout the United States evaluated over an 18-month period detected some fascinating results. The companies wanted to review the original contract, scope of work and pricing model compared to the current actual operational performance.
The Material and Information Flow Analysis (MIFA) tool was created and developed as a part of the Toyota Production System (TPS). This tool was designed as a high level and glorified Value Stream Map to analyze the material and information flow before launching a new product or program within their plant. We modified this tool and developed a software program to support current and long-time running manufacturing and distribution center analysis. Quite honestly, the results and outcome from the evaluations were nothing short of spectacular.
Analyze the Variation in Processes Which Occur Over Time
A core aim of the project was to evaluate the operational processes and compare the original “plan” against the “actual”. Over time, turnover in leadership and associates within the process coupled with scope creep can create a significant deterioration of profit or margin. Processes will deteriorate without pressure, and the focus of our MIFA is to realign the process and deploy leading KPI’s to follow. This will keep the pressure on the process going forward and alert the variation and scope creep immediately to the leadership team.
The MIFA will analyze the following areas within an operation:
- Review the original contract, scope of work and price model.
- Process Map the entire operation with on-floor evaluation (material and information)
- Evaluation of Space Utilization and calculate “non-value” percentage, and storage capacity.
- Equipment usage and OEE of material handling equipment (route analysis, pallets per hour …. etc.)
- Labor utilization (direct and indirect)
- Consumable Material usage
- Shift patterns (lunch, breaks, shift kick-off meetings, lean and clean time … etc.)
- Communication Boards (KPI’s, Problem Solving Activity, General Communication)
- Load Cubing and shipping plans
- Packaging standards (box, tape, pallets, blocking …. etc.)
- Start-up cost (if applicable)
- System utilization (WMS, InSequence, ERP …. etc.)
- Quality Control and Control of non-conforming material.
Pozyx has provided us a tool that we can deliver innovative solutions and analysis to our customers. Our previous experience with manual data collection would take several weeks to prepare and several engineers on site for a couple of weeks to collect the data, followed by a couple of weeks to analyze the data and prepare it for review and straight forward understanding from the customer.
Pozyx indoor positioning coupled with the Pozyx data platform has significantly automated this process and even provides a real time monitoring and dashboard capability for daily use.
Transparency and Manual Data Collection.
Transparency
It is critical to establish a level of trust with any organization when you need to review and analyze sensitive data. This information is typically kept very close and confidential and for the most part, not even shared with internal team members. For the MIFA to be the most effective and deliver impactful results, we must be able to compare the actual operation against the original planned operations. In some cases, we have found the current leadership team has never reviewed the original scope of work, contract, or pricing model. It becomes our job to track down this information, review, summarize and share. A high level of trust must be established for the company to share this type of information and have confidence, this data will only be used and shared with them internally.
Manual Data Collection
To establish a true picture of the current operations, a significant amount of data needs to be collected over all of the operating shifts. Time studies, equipment utilization, material storage amounts and space used, incoming and outgoing truck load density, labor utilization (both direct and indirect) all must be collected manually. Review of work instructions and training records, consumable material usage, again all manually reviewed.
All this manual data collection, over all working shifts is time consuming and requires a significant amount of labor hours. Speed and accuracy are critical elements for delivering a quality MIFA with results which are measurable and actionable, all at a reasonable price with little to no risk.
Pozyx RTLS Wireless Kit
Pozyx RTLS is one the most accurate and reliable systems on the market. It is very easy to learn and operate the software and can be set up and running within a few days. Our issues was, we did not need to have a permanent installation, we need to have a fast installation and portable system we could move from location to location. Pozyx engineers went to work and quickly designed a portable and wireless system that can be up and collecting live data in less than 10 minutes. We can cover almost 2000 m2 (21,500 ft2), using 6 wireless anchors and 10-20 trackers.
By leveraging the Pozyx wireless technology, we are able to collect real-time data, across numerous shifts, 24/7 if necessary, using very limited number of labor hours. This technology has improved our speed of data collection by over 100%, providing significantly more data points than we could ever collect manually. Coupled with the Pozyx Software Platform, we are able to analyze equipment utilization per zone, labor utilization, time studies, workflow balance, and workflow routes, pallets moved per hour and truck load density, all at the same time. This wireless solution has been a game changer for performing and analyzing critical operational performance data. Allowing us to go from performing about 1 MIFA per month, to in some instances 3 per month.
“Customer is the Hero of the Story”
Delivering results of an analysis comparing the actual performance of an operation against the original plan can be very stressful for the existing management team. They often have the feeling the results are somehow a representation of their current management and/ or lack thereof. However, it is impossible for them to know what they do not know and what has not been shared in detail with them. This variation is often the result of many years of scope creep initiated in small doses over time and the compilation of processes which have not had pressure (processes will deteriorate over time without pressure).
We are frequently asked why our team can find these variations, analyze them and determine a solid action plan with deliverables and the local team cannot. The answer is actually quite simple, it is our sole objective and focus. We do not have to worry about attendance, equipment down, executive team visits, meetings, customer visits or any daily delivery issues. We can tone all of those things out and focus on data collection and analysis.
A part of creating trust with the organization, we must always make them (the leadership team) look good, making them the hero of the story. It is critical to not only show the variation, but also why the variation is present and a solution of how to correct. Allow them to present the results to the executive team, and to show this is why they connected with P3T, LLC to carry out such a study. “Every story can have only one hero” (Building A Story Brand, Donald Miller)
Summary of MIFA results
- Direct labor overage it typically due to scope creep.
- Indirect labor overage is typically due to original plan/ pricing model.
- 73% of forklift run time is carrying only air.
- Large increase in consumable cost due to original pricing model, material cost increase and no KPI measuring as a whole.
- Unit pricing scenarios (sequence centers, pallet in/ pallet out, pallet storage … etc) use significantly higher storage space than planned.
- Equipment overage is usually caused by a special event (single point need and not returned)
- Contract and Scope of Work are very rarely reviewed.
The most common area of risk, we found in every site we have performed the MIFA, the lack of leading KPI’s to monitor and keep pressure on the process. We have not found any location in all our reviews which had clear and precise leading KPI’s. These are crucial to allow management to measure and adjust prior to a negative P&L impact.
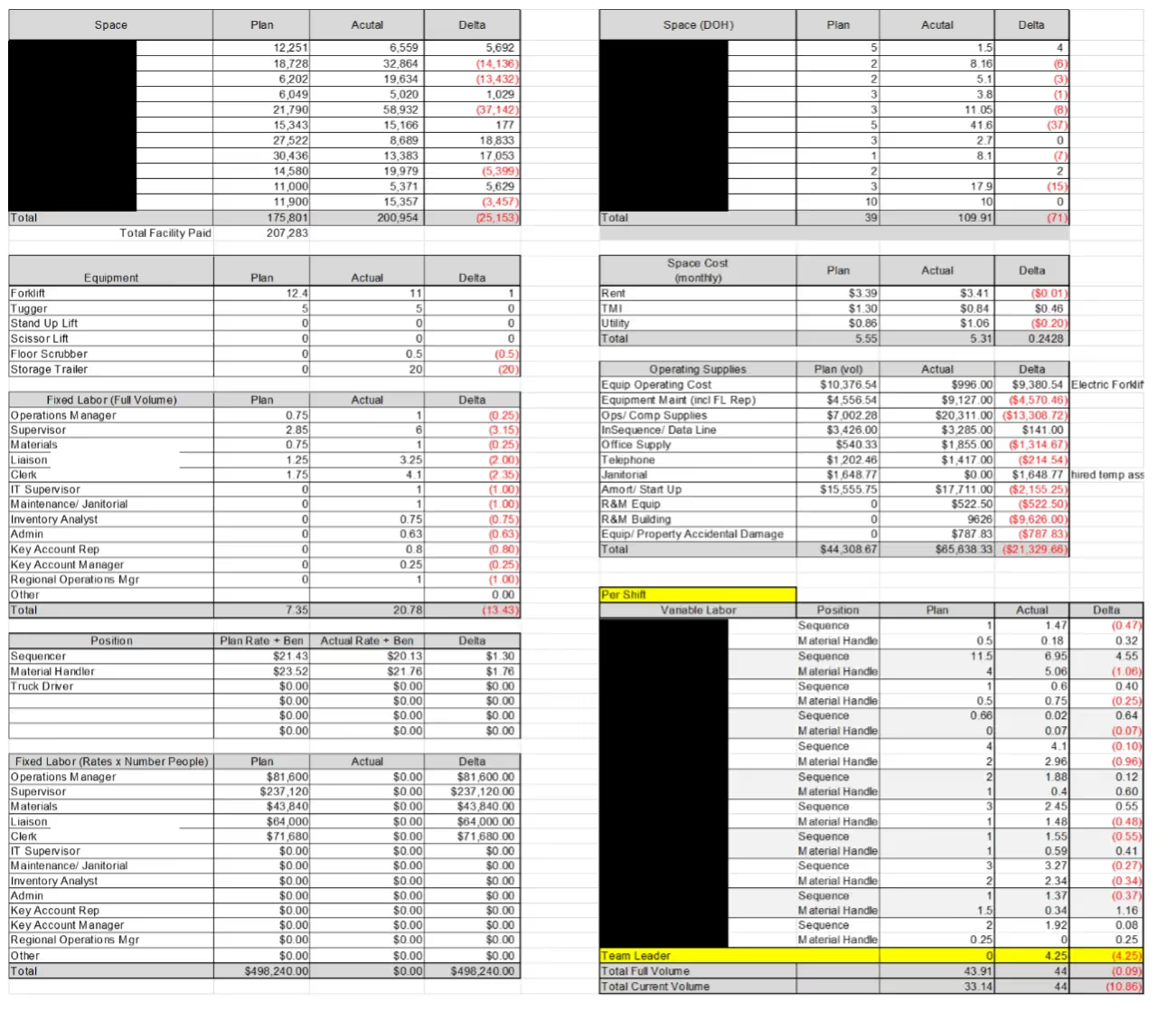
Key Factors for Choosing Pozyx
- Pozyx UWB based technology delivers high levels of accuracy and precision.
- The wireless technology is unmatched in UWB sector.
- Uploading floor plans and creating geo zones is simple and fast, resulting in minutes from start-up to collecting live data.
- Extremely long battery life of trackers
- Dedicated engineering support
- Platform Analytics (Spaghetti Diagram, Heat Maps, Process Flow Mapping, Behavior Analytics) are all standard.
- Creating and sending alerts are standard and easy to select from a drop-down style menu.
- Open API allows for direct integration between our database and Pozyx database.
- On premise or cloud Platform for security control or remote analysis support.
Do you struggle with collecting the data for a MIFA? Or do you want to perform a MIFA? Schedule a call with our experts to discuss your use case, we are happy to help!